How can mold flow analysis improve plastic injection molding?
- Optimize Gate Positioning
- Identify and Predict Fill Patterns
- Predict Part Deformation
- Improve Overall Product Quality
- Create New Design Adjustments and Solutions
The plastic injection molding process allows manufacturers to create a wide array of high-quality processes. It can also give you the ability to mass-produce products in large numbers and at a shorter period of time. It is important to maintain this process as any problem or mistake can compromise the whole process entirely. This is where Mold Flow Analysis comes in.
At times, most of the problems stem from the mold design process as there can be issues that can greatly affect the quality of the final product. It is important to solve these problems as soon as possible, and the best solution is to make use of systems like Mold Flow Analysis.
What is Mold Flow Analysis?
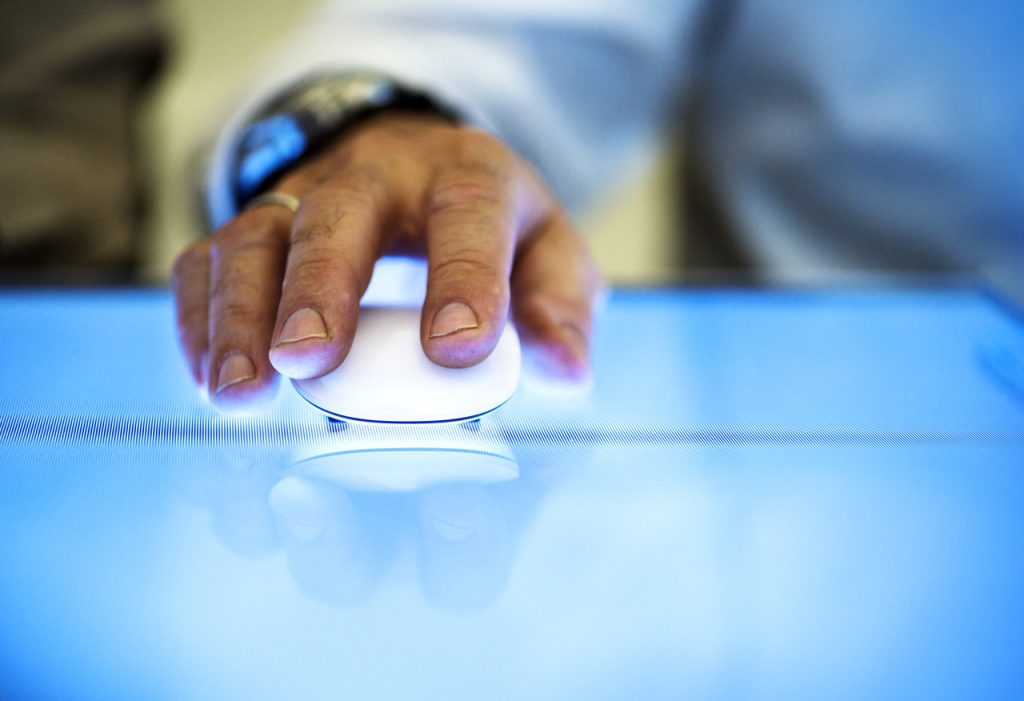
Mold Flow Analysis is a software that is designed to predict and simulate the flow of plastic during the injection molding process. It enables plastic manufacturers to see the effectiveness of their mold design and see how it all flows together before even trying it out on the machine itself.
Creating and designing a plastic product is a process that requires a good amount of testing and experimentation before manufacturing. Having software such as Mold Flow Analysis helps save more time, resources, and production costs by having the ability to analyze the success and effectiveness of a plastic mold.
How does Mold Flow Analysis improve Plastic Injection Molding?
The implementation of Mold Flow Analysis has helped improve the plastic injection molding industry. It has provided a set of advantages and functions that help optimize how plastic products are manufactured. There are many ways that you can utilize Mold Flow Analysis in your manufacturing and design process. Here are some of the ways it can improve your overall manufacturing capabilities.
Optimize Gate Positioning
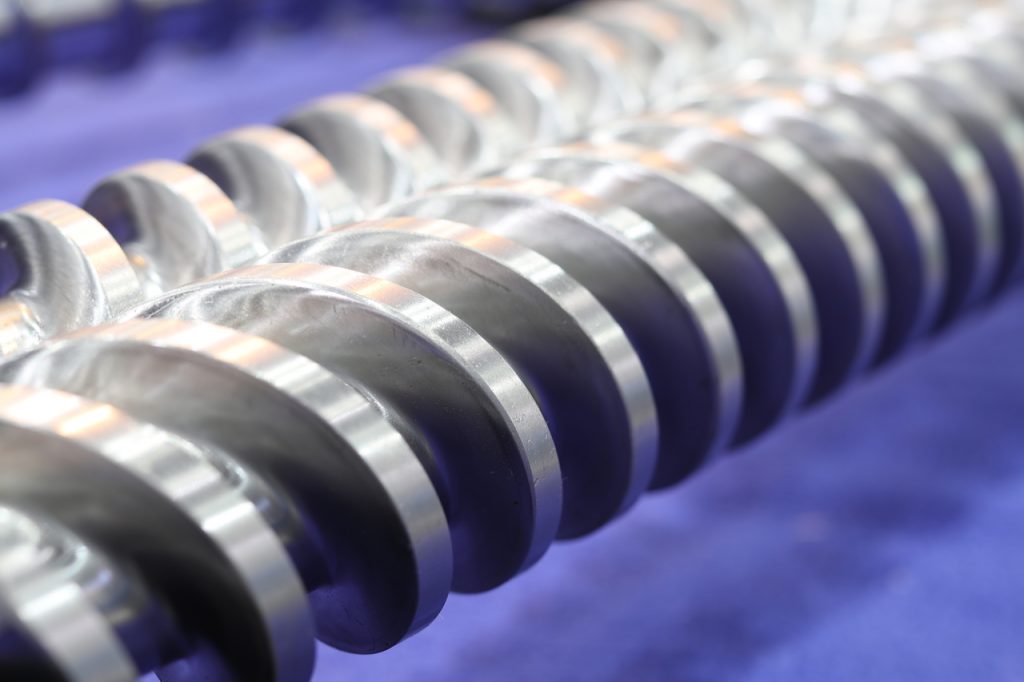
Gate positioning is crucial in the plastic molding process as they are the entry points for molten plastic to enter and create the final product. Improper gate positioning means that there can be some sections that would not be filled correctly. This means that the product might be incomplete due to not enough plastic flowing to it. Through the use of Mold Flow Analysis, you can find the right positions for each of your gates and ensure that plastic enters the mold evenly and efficiently.
Identify and Predict Fill Patterns
Along with identifying the correct gate positions, Mold Flow Analysis can also identify and predict fill patterns. This function simulates how the molten plastic would flow into the mold, allowing you to have a good idea of how your final product would look like. These fill patterns will help you see if there are sections that do not get enough plastic during the molding process. This is a sign that redesigning the mold must be done to optimize the operations.
Predict Part Deformation
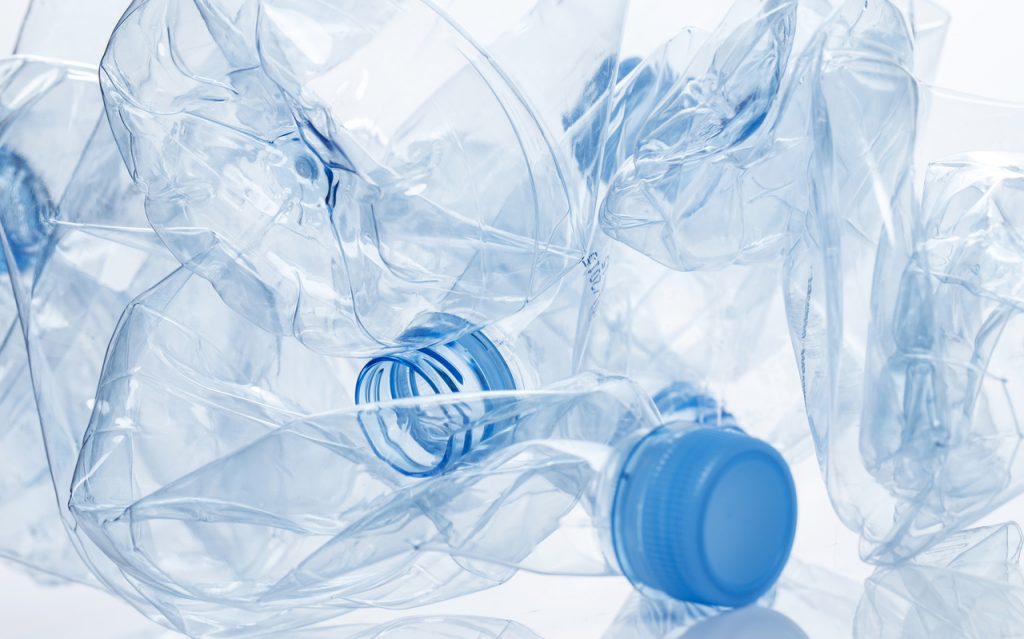
Product defects are errors in the design process that can be very costly. Manufacturing multiple defective copies will result in having to produce the same parts again. This takes away a lot of resources, which is a scenario that you would want to avoid at all costs.
By using Mold Flow Analysis, you can predict which areas in your mold design would most likely cause defects during production. This will allow you to solve them immediately. Any type of deformation or defect can greatly compromise the quality and durability of any plastic product. This is why Mold Flow Analysis is key, to prevent these mistakes from happening in the first place.
Improve Overall Product Quality
One of the biggest advantages of using Mold Flow Analysis is that you will be able to improve the quality of your products. Having the ability to predict how plastic flows through your mold allows you to make the necessary adjustments and create improved designs before production even starts.
Plastic injection molding allows you to create a huge number of high-quality products on a consistent basis. Using Mold Flow Analysis will help make sure that this process remains streamlined and efficient, which in turn lessens the number of errors and issues present.
Create New Design Adjustments and Solutions
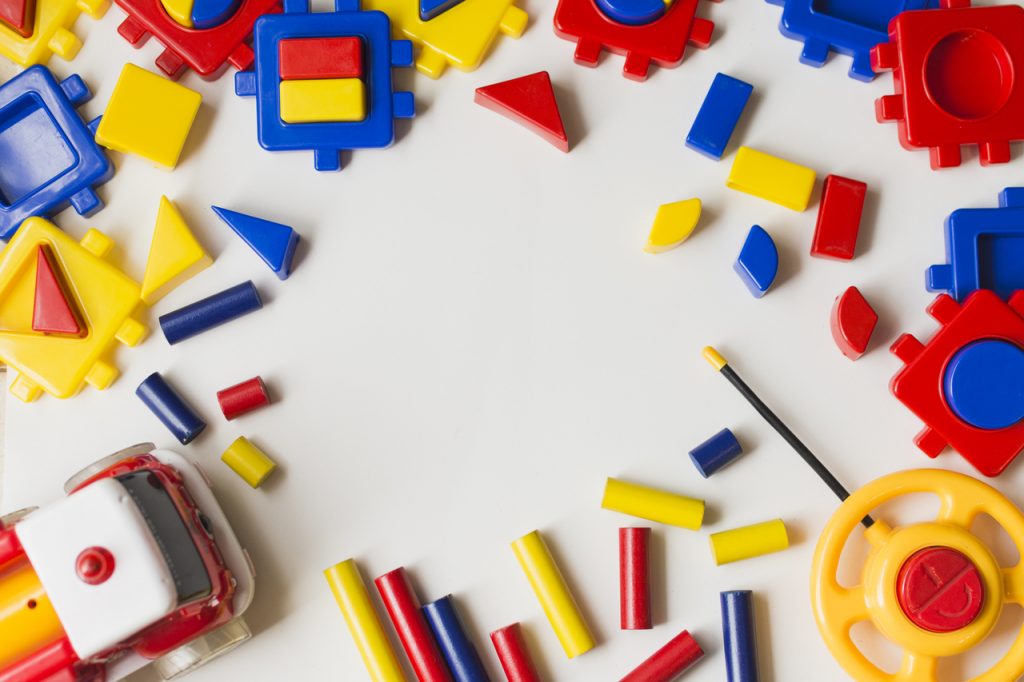
Mold Flow Analysis is a software that helps you minimize the number of mistakes and errors during the mold design process. This allows you to create products that have the highest quality. This means that you have the ability to create a diverse array of new designs. Easily find new adjustments and solutions that help improve your final design.
Key Takeaway
Plastic injection molding is a process that is designed to maximize quality and design. Systems like Mold Flow Analysis has the ability to minimize errors and create better products and designs overall. With these advantages, you can make sure that you improve your overall production process and find new ways to create products.