What is the importance of mold design in injection molding?
- Ensure high tolerance
- Eliminate defects
- Determine project feasibility
- Choose the right raw materials
- Predict environmental behavior
Everyone in the injection molding industry understands the importance of mold design. As you may know, the mold is the component in plastic injection machinery that determines the appearance and quality of the finished product. This part works together in conjunction with the rest of the components — like runners, gates, sprues, and heat chambers — to produce a high-quality plastic product.
Keeping this in mind, manufacturers work tirelessly to craft a mold design that meets not only design specifications but also customer expectations for both high and low-cavitation injection molding. The quality and make of the mold allows injection molders to ensure high tolerance, identify defects, maintain precision, choose the right raw materials, as well as, predict the behavior of the product during end-use. After all, only a well-designed mold is capable of satisfying the different standards expected from an injection molding company, Continue reading to learn more.
Ensure High Tolerance
In manufacturing, tolerance is defined as the leeway allowed between the design and the appearance/functionality of the final product. Tolerances give manufacturers a bit of legroom in making modifications. This is done to get as close to the final product as possible while satisfying the client’s demands.
Typically, injection molds are capable of achieving tolerances of 0.005 inches, give or take. However, this can differ, depending on the specifications of the client or the design of the mold. Crafting a mold design requires an understanding of the resin behavior — i.e. some resins are prone to shrinkage and minor warping during the injection molding processes. But if the tooling mold has been designed to accommodate these tolerances, resin behavior can be easily predicted. This results in a workable plastic mold that won’t have to undergo extensive post-processing.
Eliminate Defects
Some of the factors associated with injection molding defects are the following: mold design, rate of injection, pressure, temperature, runner presence, type of sprue, gate, and the like. Even if many injection molding deformations only have aesthetic implications at best, manufacturers still want to eliminate them. Flow lines and discolored portions of the ejected product are unsightly and may not satisfy the customer’s needs.
To prevent or completely eliminate these defects from happening, manufacturers need to make a series of changes to the injection mold machine or CNC equipment they use. For example, they may need to change the wall thickness of the tooling mold or create rounded corners in order to improve the flow consistency of the molten resin. They may also need to completely redesign the entire tooling mold just to make its shape more symmetrical.
Determine Project Feasibility
All other factors aside — injection speed, cooling rate, type of thermoplastic/resin — mold tooling are essential in maintaining the precision design in final injection molded products. As manufacturers try to be receptive to the requests of their clients, they also need to consider the injection molding production process as a whole. The mold design determines precision as well as the feasibility in manufacturing.
This is why injection molding companies continue to work closely with their clients to come up with different designs of a mold. Injection molders employ a range of techniques such as prototyping, reverse engineering, and CNC machining just to craft a molding die with the right dimensions, wall thickness, and cavitation.
Choose The Right Raw Materials
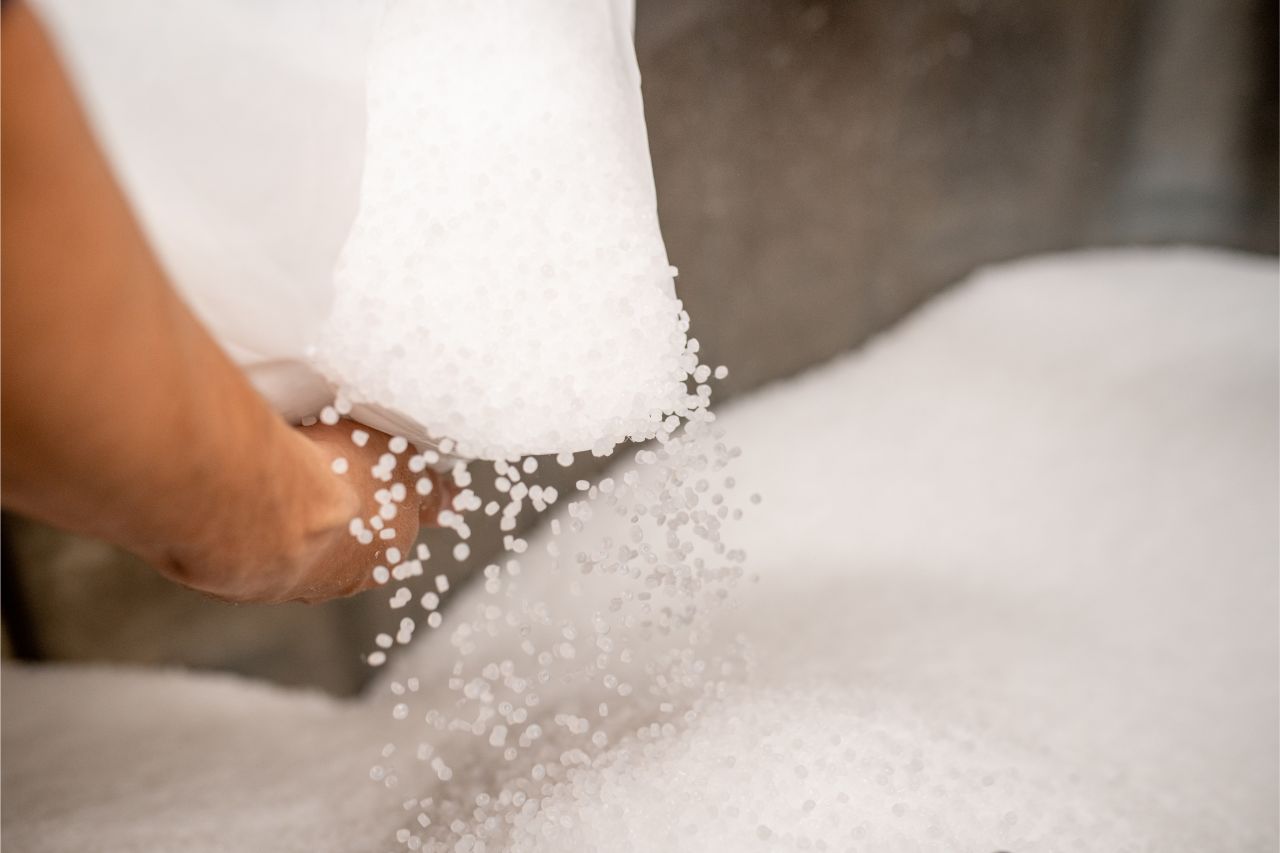
Although most types of resins can be used in injection molding, they don’t necessarily have similar qualities. As mentioned before, some plastics are prone to shrinkage, more so than others. The reasons for this is due to the difference in density when the product is in solid and molten form. This means that even when the product has already been ejected from the injection mold machine, it may continue to significantly shrink over time as it continues to cool.
To prevent extreme plastic shrinkage, mold design is modified for each kind of resin. Resins that have high shrinkages (like polypropylene) should be used in molds that do not have thick walls. In this case, each of the mold cavities have to be designed in such a way to predict the rate and gravity of the shrinkage for different polymers.
Predict Environmental Behavior
Finally, mold tooling is also important in determining the environmental behavior of the finished product. This simply means that the product still maintains its design and functionality even when exposed to the elements, whether during assembly with other components or on its own.
WIth mold design, it’s far easier to predict how an injection molded product will be affected by its surroundings. Manufacturers may need to change certain aspects of the mold tooling — whether it is by reducing the number of cavities, lowering the wall thickness, or using a different tooling metal/alloy altogether.
Key Takeaway
In this simple guide, you’ve learned the importance of mold design in injection molding. Although this is but one component in an injection mold assembly, the mold design affects the plastic product’s appearance, feasibility, environmental behavior, possibility of defects, and tolerance level. Any well-built mold can be engineered to anticipate all of these factors, allowing for a more efficient and high-quality injection molding process.
In need of a plastic injection molding company that can develop molds for your prototype? Contact Richfields Plastics now! We cater to all injection molding, prototyping, and CNC machining needs for different industries.