How to achieve proper injection molding tool transfer?
- Facilitate clear communication
- Conduct proper assessments and scheduling
- Create backstocks while in transit
- Validate the tooling
- Commence production
Anytime that a company, be it an OEM or any large manufacturing firm decides to move towards a plastic injection molder, it’s never just a simple task. Knowing how to achieve injection molding tool transfer entails that millions or parts and dollars may be spent. Since this offers any custom molder with a large base of operations, it’s no walk in the park.
Considerations should be weighed heavily, such as the capabilities of the outsourced molder/in-house facility. This could be due to a variety of reasons — the OEM may have concerns about their current mold supplier’s financial stability, or they may not be attracting customers due to price discounts offered by a competitor. Usually, however, it is due to the current molder’s inability to meet the OEM’s needs — high scrap, old molds, and cost-ineffective solutions.
Deciding to move towards a plastic injection molder becomes the best option in the scenario above. Although difficult, the right safeguards and processes can make any injection molding tool transfer smooth sailing in this circumstance. Read on to learn more.
Facilitate Clear Communication
A contractual agreement should form the basis of any injection molding tool transfer activity. This document is legally-binding and defines the commitment of both parties. It should outline that all involved parties will have their interests protected, so long as the agreement lasts.
A transfer contract should define a dedicated management team, based on the project requirements. Both firms should be willing to provide personnel or make such arrangements in that nature to ensure the success of the transfer.
Facilitating clear communication can be certainly possible by ensuring there are no lapses in the agreement as well as documentation. Since the transfer is a collaborative effort, both parties should hold the responsibility to manage aspects of the transfer, such as equipment, date of transport, quality of machinery, manpower, and so on.
Conduct Proper Assessments and Scheduling
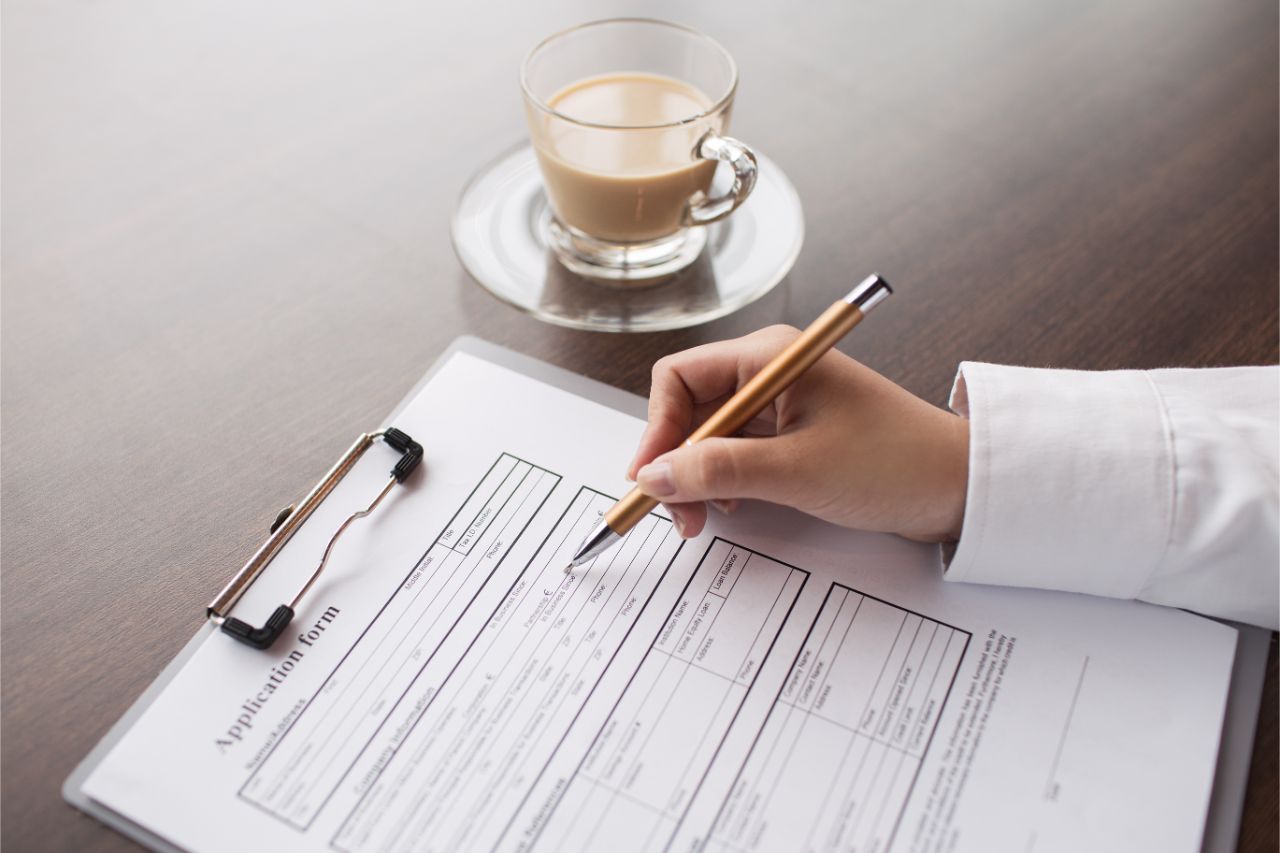
Any molding company will house a variety of molding machines, press brakes, or CNC machinery. Other machinery may also be present, such as hydraulic, electric injection molding, hybrid injection molding equipment, and the like.
With these in mind, it’s essential that proper assessment and evaluation of all tools and machinery are done at the current location. This allows the plastic molder to fully understand any eccentricities or nuances in the tool, discovered through the evaluation process. This is done to make the logistics much simpler and prevent any issues that might hamper the safe transfer of the machines.
Once proper evaluations have been completed, both companies must be able to schedule the date of the transfer. Oftentimes, this date is also explicitly stated in the contract. If either one of the parties fail to meet this, there could be legal ramifications or the transfer process could meet unexpected obstacles along the way.
After conducting assessments, it is crucial, therefore, to immediately provide a date that both parties must agree to. This speeds up the transfer process and reduces any delays that may potentially affect the validity of the contract.
Create Backstocks While in Transit
Unexpected obstacles and situations could take place during mold tooling transfer. One of which is the unintended damage of the equipment that may reduce the stock of parts in transit to the new location. To mitigate this, it’s crucial that both firms agree on creating backstocks and a sufficient amount of parts as a safety stock to cover any lapses.
The time frame allotment for producing safety stocks will depend on the contractual agreement. But it is typically advised to have this done within a six-week period. As part of the validation process, the goal for the back stocks is to showcase the success of the transfer. Not only this, but it is one way to determine if the sample stocks are up to par with the client.
Validate the Tooling
Validation and back stock production may come hand in hand, as both of these determine how well the tooling equipment will be able to meet the customer’s needs. It’s essential that the tooling transfer process does not skip this step, as a way of evaluating not just the quality of the equipment but also the long-term benefits of the transfer.
Validation is crucial for industries that have specific requirements. Some examples include medical, automotive, and construction where product design and precision should be able to satisfy high tolerances as much as possible.
This process can be done either in-house or through a third-party molder, depending on the arrangement. Nevertheless, the validation must be repeated in the same press to be used after installing the mold in the production molding facility. Criteria for validation may also vary, but it will generally conform to DPA or PPAP standards, Whatever the case, the same machinery is always used.
Commence Production
Once the manufacturing plant has been fully debugged, tooling materials have been transferred, production is ready to begin. The machinery will be handled by manual operators and supervised by a number of managers that inspect tooling. They will also have to oversee the project, establish manufacturing processes, and determine other requirements deemed necessary.
Overall, when the entire tool transfer process has been supervised accordingly and properly, proper production will transpire with little issues. The plant is ready to provide custom molded plastic parts to clients.
Key Takeaway
Understanding the basics of how to achieve injection molding tool transfer is critical to the success of the operation. It always starts off with defining a legal contract that sets the terms of agreements for the transfer. This outlines the capacity of the new molder and OEM/firm to agree on the right project personnel for the transfer, as well as the ability to create backstocks and validate the machinery.
The endpoint of any successful mold tooling transfer is always production. When all machinery, press brakes, tooling dies, and CNC equipment have all been transferred to the new plastic molder, then production of custom plastic parts can now be done.