What are the reasons to consider metal to plastic conversion?
- Less Expensive
- Lighter Weight
- Better Performance Attributes
- Greater Design Flexibility
- Faster Assembly
- Offers More Material Choices
There is the misconception that there are “metal applications” and “plastic applications” in manufacturing. However, you can change part and product design to incorporate plastic in typical “metal applications” nowadays. There are many reasons to consider metal to plastic conversion for your production. Depending on your product, if the choice is plastic vs. metal, plastic could be the better choice.
Whether you’re currently considering making the shift, or merely just looking for viable options for your project, here are some advantages of switching to plastic to keep in mind.
Less Expensive
In general, raw plastic material is less costly than raw metal material. Depending on the volume and material in use, plastics can also be easier to source and procure for your project — shortages for these materials are practically non-existent. The same can’t be said for raw metal, whose prices and availability fluctuate according to the market’s supply and demand.
In some cases, manufacturers don’t have the luxury of waiting for the metal to drop to more affordable prices or for the material to become available, so plastic could be a good option for them.
Plastic manufacturing is also generally more streamlined and efficient than metal manufacturing processes. Plastic is usually manufactured via plastic injection machines, which can create multiple pieces at once with less waste — thus reducing material waste and lessening overall costs.
Lighter Weight
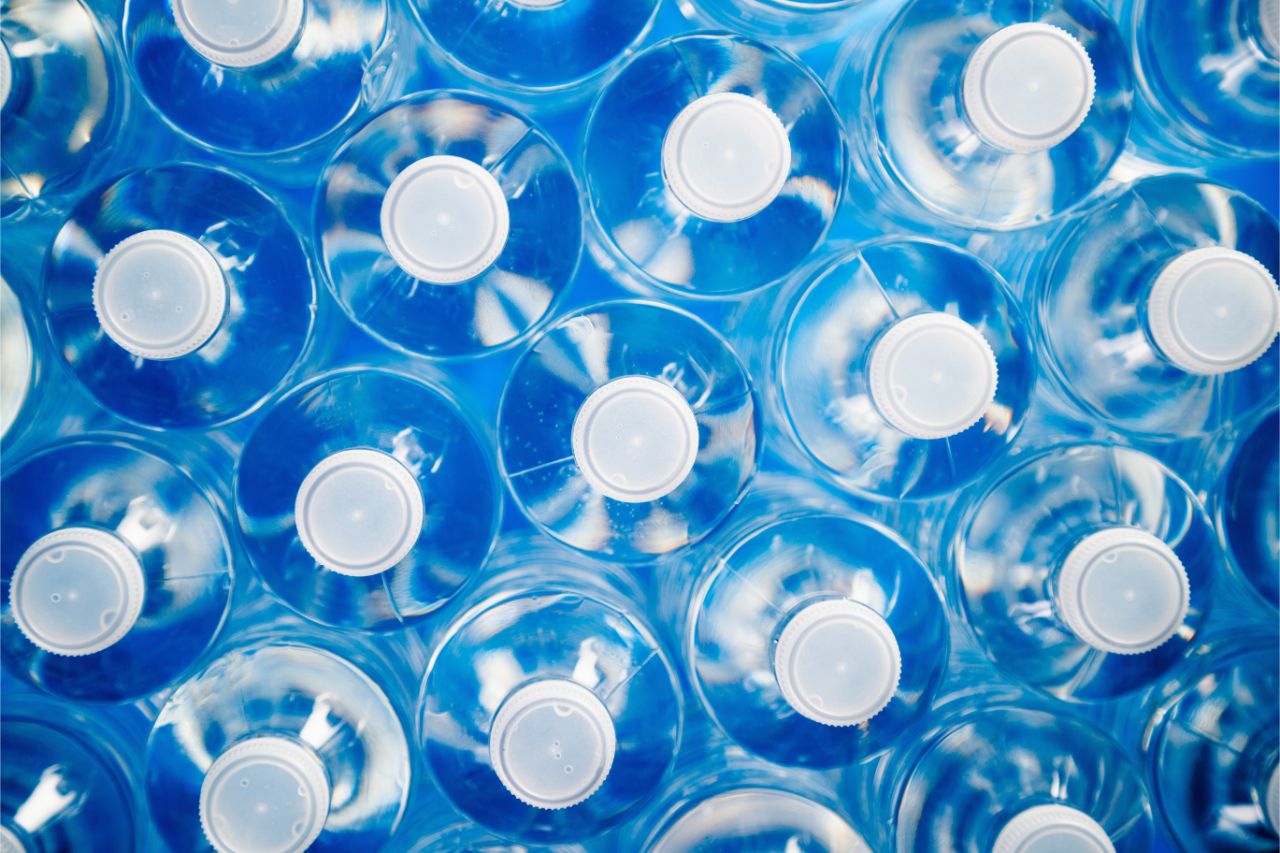
While it might not seem like a big deal to the layman, weight is a big factor when considering what materials to use for production. This simple benefit is one of the reasons that many manufacturers make the switch to plastic. This is due to the weight of the material factoring into costs for manufacturing, shipping, and the end applications of the product.
When it comes to manufacturing, sourcing costs become lower the lighter the material is. This is because lighter materials can be transported to the manufacturer much more easily. Shipping costs to customers become lower for the same reason as well.
Weight will factor in how the product will be able to meet the expectations and requirements of the end application as well. Plastic products can be made to be lighter, smaller, and thinner than metal products. This means it can better meet the size and weight restrictions for certain appliances, engines, medical equipment, and more.
Better Performance Attributes
The properties of plastic result in certain performance attributes that metal simply can’t beat. There are plastic materials that offer higher tensile strength, increased durability, and resistance to impact, corrosion, and heat. Additionally, these natural properties of plastic can be improved with new blends and hybrid formulations available in plastic production.
Tensile strength is a key requirement when considering what components to use in end products like vehicles and tools. This property is needed for products that are subjected to substantial, repetitive stress. The strength and rigidity of plastic can exceed that of metal, which makes it a more attractive option.
Not only can plastics withstand a considerable amount of stress, but they can also withstand other extreme environmental factors. Even when subjected to these factors, plastic parts can hold tight tolerances. This makes plastic just as durable and robust as traditional metal parts.
Plastic is also naturally resistant to impact and corrosion by nature, while most metals need to undergo a coating or spray process to achieve the same property. Plastic can also be designed to meet specific performance requirements. Many plastic blends increase heat resistance, which makes them ideal for more demanding applications.
Greater Design Flexibility
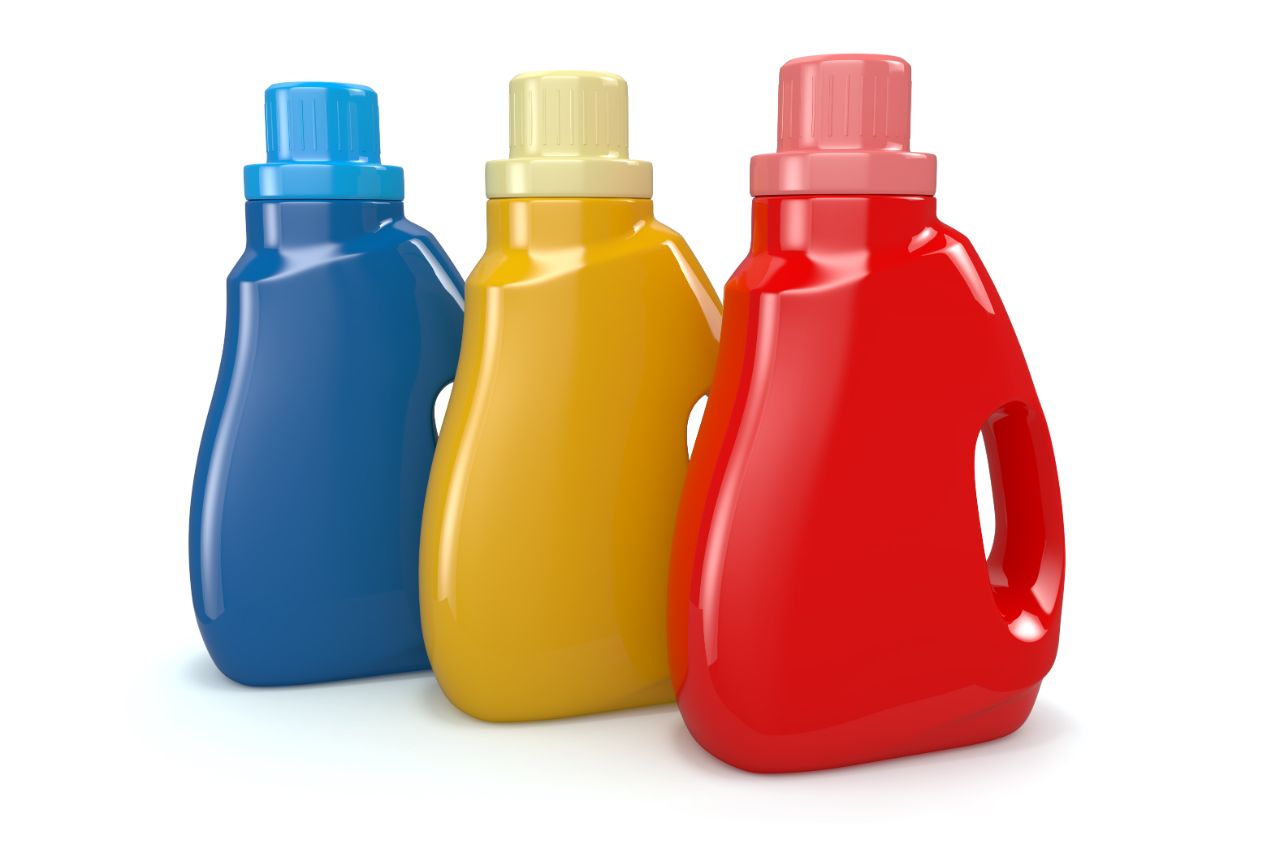
Metal manufacturing has a limited range of processes it can apply efficiently. This means that more complex designs using metal materials undergo exponentially more processing, which increases manufacturing time and costs.
Plastic manufacturing does not encounter the same problem. This is because this process utilizes injection molds, which allow for a broader range of design choices in just one step of the process. When looking at the differences in time and cost between molding a simple design versus a complex one is nearly negligible.
Faster Assembly
Due to its flexibility, plastic manufacturing can also do several assembly processes in one go. This means that plastic parts don’t have to go through the process of being made piece by piece, then being welded or assembled into a final product.
Instead, plastic components are made in one piece using one plastic mold. These components can be used right out of the machine, without the need for finishing or additional processing.
Additionally, unlike metal tooling, plastic tooling can last a long time without needing to be replaced. While creating the tools used for metal and plastic parts tend to be quite similar, the tools made for plastic molds have longer lifespans. In fact, plastic tools have ten times the life expectancy of a cast aluminum tool. This means that production and assembly for plastic components can continue without interruption for long periods.
Offers More Material Choices
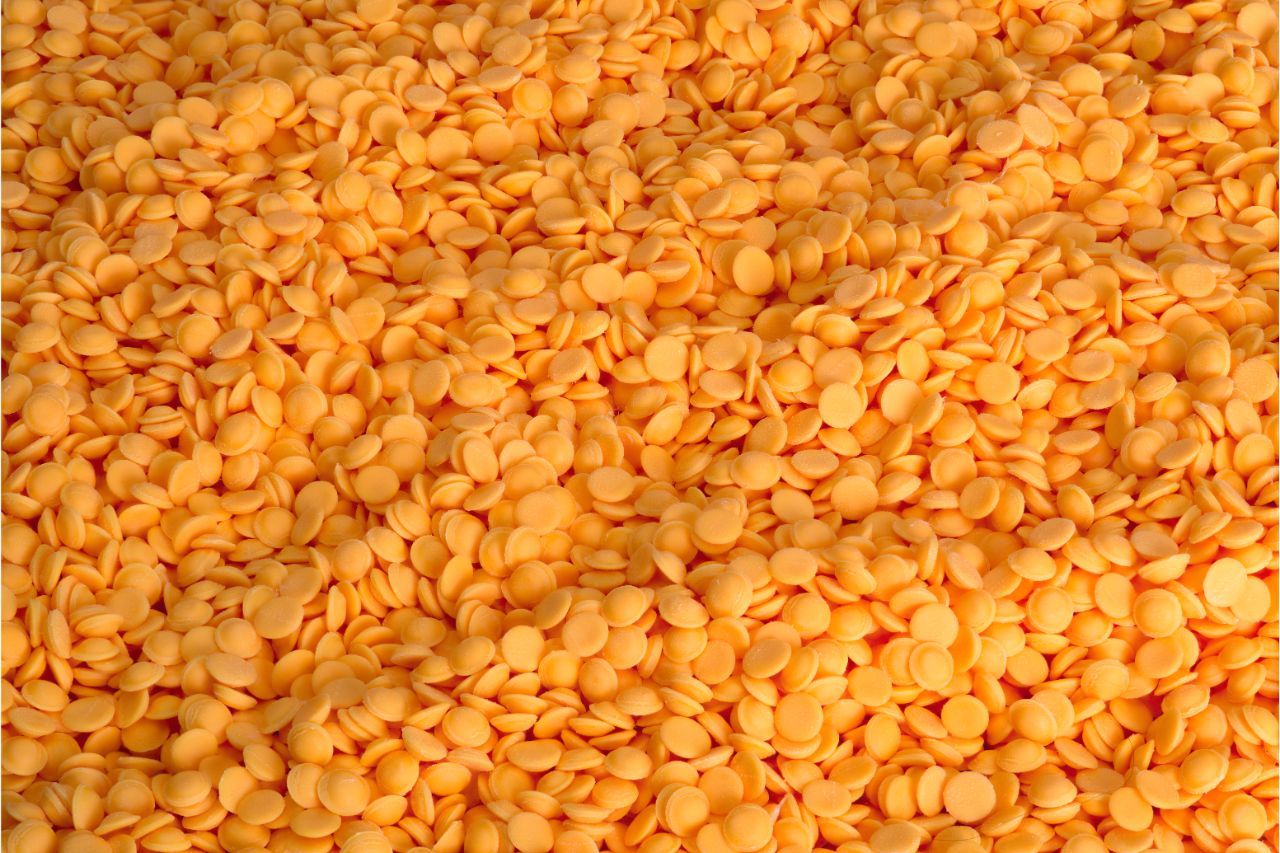
Plastic material choices are nearly endless — custom plastic materials can even be made for your project. These can be procured or designed extremely easily, which makes them suitable for projects looking to make a product with specific properties.
While metal has a considerable number of alloys, it is still relatively limited to the number of plastic materials available to the market. If your project has unique requirements and you’re working with metal alloys, there is a greater chance that you’re unable to find one that can meet the desired properties for your application.
Key Takeaway
Due to its many benefits, there are several reasons to consider metal to plastic conversion. When considering plastic for your manufacturing process, it is vital to contact an experienced injection molding company to assist you in making the switch. With Richfields, you will have experts helping you to improve your design, as well as provide the right tools to ensure that you receive the best parts for your product. Contact us today to avail of their consultation and services!